Addressing Challenges In Automated Visual Inspection Of Lyophilized Vials
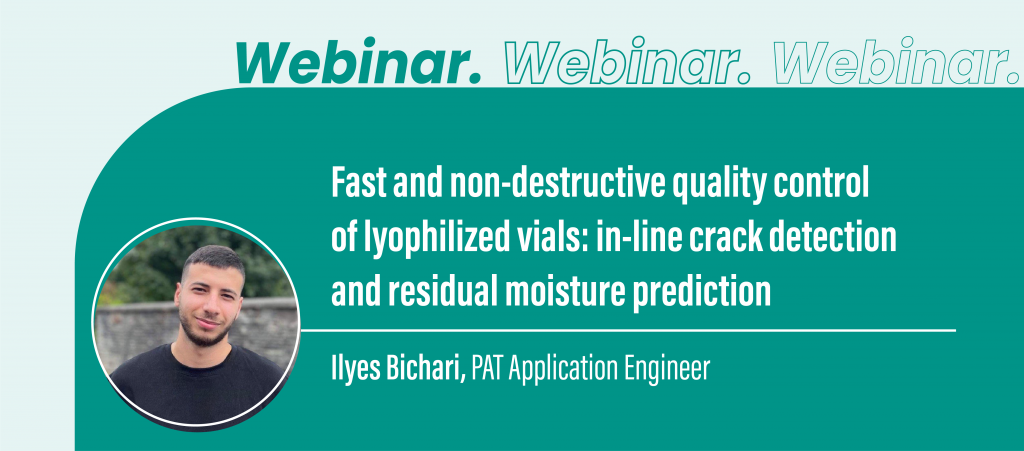
Table of Contents
Challenges Related to Image Acquisition and Preprocessing
The inherent variability in the appearance of lyophilized cakes within vials presents significant hurdles for automated visual inspection systems. Consistent and reliable image acquisition is crucial for accurate defect detection, yet achieving this consistency is often difficult.
Variations in Vial Appearance
Lyophilized cakes exhibit a wide range of appearances, including cracks, collapses, variations in cake height, and surface imperfections. These variations significantly impact the effectiveness of automated inspection.
- Uneven illumination: Variations in lighting can create shadows and obscure defects.
- Reflections from the vial surface: Glare and reflections can mask subtle imperfections within the lyophilized cake.
- Variations in cake color and texture: Differences in color and texture can make it difficult for algorithms to consistently identify defects.
Addressing these challenges necessitates advanced lighting techniques and sophisticated image preprocessing algorithms. For example, polarized lighting can minimize reflections, while shadow removal algorithms can enhance image clarity. Careful consideration of lighting angles and intensities is critical for optimizing image quality for automated visual inspection.
Detecting Subtle Defects
Small cracks, particulate matter, or slight discoloration are often difficult to detect reliably with automated systems. The ability to identify these subtle defects is crucial for ensuring product quality and preventing potential patient risks.
- Resolution limitations of cameras: Low-resolution cameras may miss small defects.
- Sensitivity to noise: Noise in the image can interfere with accurate defect detection.
- Need for high-contrast imaging: High-contrast images are essential for highlighting subtle differences in color and texture.
Overcoming these challenges requires high-resolution cameras and advanced image analysis algorithms. Sophisticated algorithms, potentially incorporating machine learning techniques like convolutional neural networks (CNNs), are needed to enhance sensitivity and specificity in identifying subtle defects. Careful calibration and optimization of the imaging system is essential for optimal performance.
Algorithm Development and Implementation Challenges
Developing robust and reliable algorithms for the automated visual inspection of lyophilized vials presents significant complexities. Furthermore, integrating these systems into existing production lines requires careful planning and execution.
Developing Robust Algorithms
Creating algorithms that accurately identify a wide range of defects with minimal false positives and negatives is challenging due to the inherent variability in lyophilized cake appearance.
- Need for extensive training data: Robust algorithms require vast datasets of images with accurately labeled defects.
- Handling variations in vial shape and size: Algorithms must be able to handle variations in vial geometry and dimensions.
- Dealing with occlusions: Occlusions, where defects are partially hidden, can complicate defect detection.
The development of such algorithms typically involves machine learning techniques. Data augmentation, where existing images are modified to create additional training data, can improve the robustness and generalizability of the algorithms. Careful model selection and rigorous testing are crucial for ensuring high accuracy and reliability.
Integration with Existing Production Lines
Integrating automated inspection systems into existing production lines can be disruptive and costly. Careful planning and execution are crucial to minimize downtime and maximize efficiency.
- Compatibility issues: The automated system must be compatible with existing equipment and software.
- Workflow changes: Implementing the new system may require changes to existing workflows.
- Validation requirements: Regulatory compliance demands thorough validation of the automated system.
A phased approach to integration, with thorough planning and risk assessment, is recommended. Collaboration between engineering, production, and quality assurance teams is vital for successful implementation and minimization of operational disruptions.
Regulatory Compliance and Validation
Meeting regulatory standards for automated visual inspection systems is paramount for ensuring product safety and regulatory compliance. This involves rigorous validation and documentation procedures.
Meeting Regulatory Standards
Automated inspection systems must meet stringent regulatory requirements for accuracy, reliability, and data integrity.
- Validation protocols: Thorough validation protocols are required to demonstrate the system's performance.
- Documentation: Detailed documentation is crucial for compliance purposes.
- Traceability: Complete traceability of the inspection process is essential.
Compliance with guidelines such as GMP (Good Manufacturing Practices) and 21 CFR Part 11 is mandatory. This necessitates detailed validation plans, comprehensive documentation, and rigorous testing to demonstrate that the system consistently meets predefined performance criteria.
Data Integrity and Traceability
Maintaining accurate records and ensuring traceability throughout the inspection process is critical for regulatory compliance and potential investigations.
- Data logging: All inspection data must be logged securely.
- Audit trails: Complete audit trails must be maintained to track changes and modifications.
- Secure data storage: Data must be stored securely to prevent unauthorized access or modification.
Robust data management systems are essential for maintaining data integrity and meeting regulatory requirements. These systems must be designed to ensure data security, accuracy, and accessibility for auditing purposes.
Conclusion
Automated visual inspection of lyophilized vials offers significant advantages in terms of quality control and efficiency, enhancing product consistency and minimizing the risk of defects reaching the market. However, successfully implementing such systems requires addressing the substantial challenges related to image acquisition, algorithm development, and regulatory compliance. By employing advanced imaging techniques, robust machine learning algorithms, and a thorough validation process, the pharmaceutical industry can leverage the benefits of automated visual inspection to enhance the quality and consistency of lyophilized products. Investing in advanced solutions for automated visual inspection of lyophilized vials is essential for ensuring product quality and meeting stringent regulatory requirements. Contact us today to learn more about improving your automated visual inspection processes and minimizing risks associated with manual inspection methods.
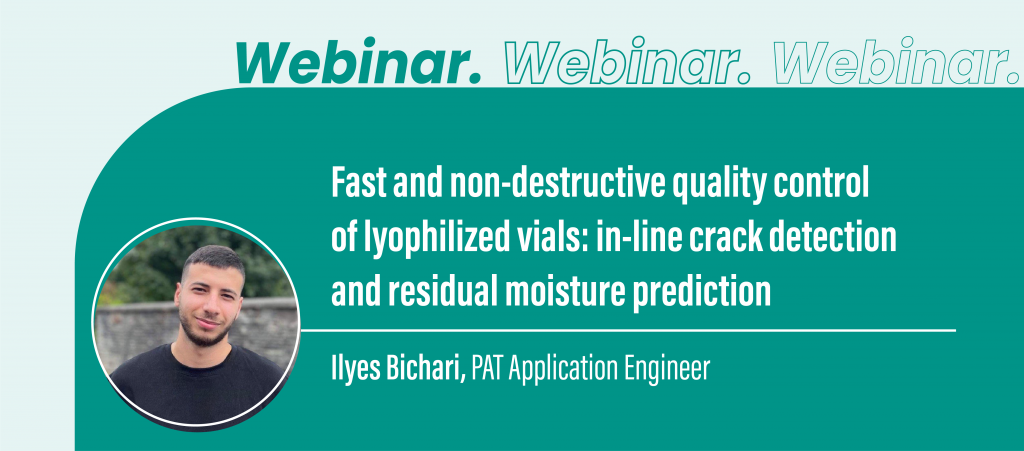
Featured Posts
-
Mlb Speedway Classic At Bristol Manfreds Fan Attendance Outlook
May 11, 2025 -
Ufc 315 Aftermath Shevchenkos Potential Superfight With Zhang Weili
May 11, 2025 -
Conclave 2024 Analyzing The Leading Candidates For The Next Pope
May 11, 2025 -
La Nouvelle Vie Amoureuse D Eric Antoine Apres Son Divorce Une Revelation Sur M6
May 11, 2025 -
Payton Pritchards New Shoe Deal Celtics Star Joins Converse
May 11, 2025