Automated Visual Inspection Of Lyophilized Vials: A Comprehensive Guide To Troubleshooting
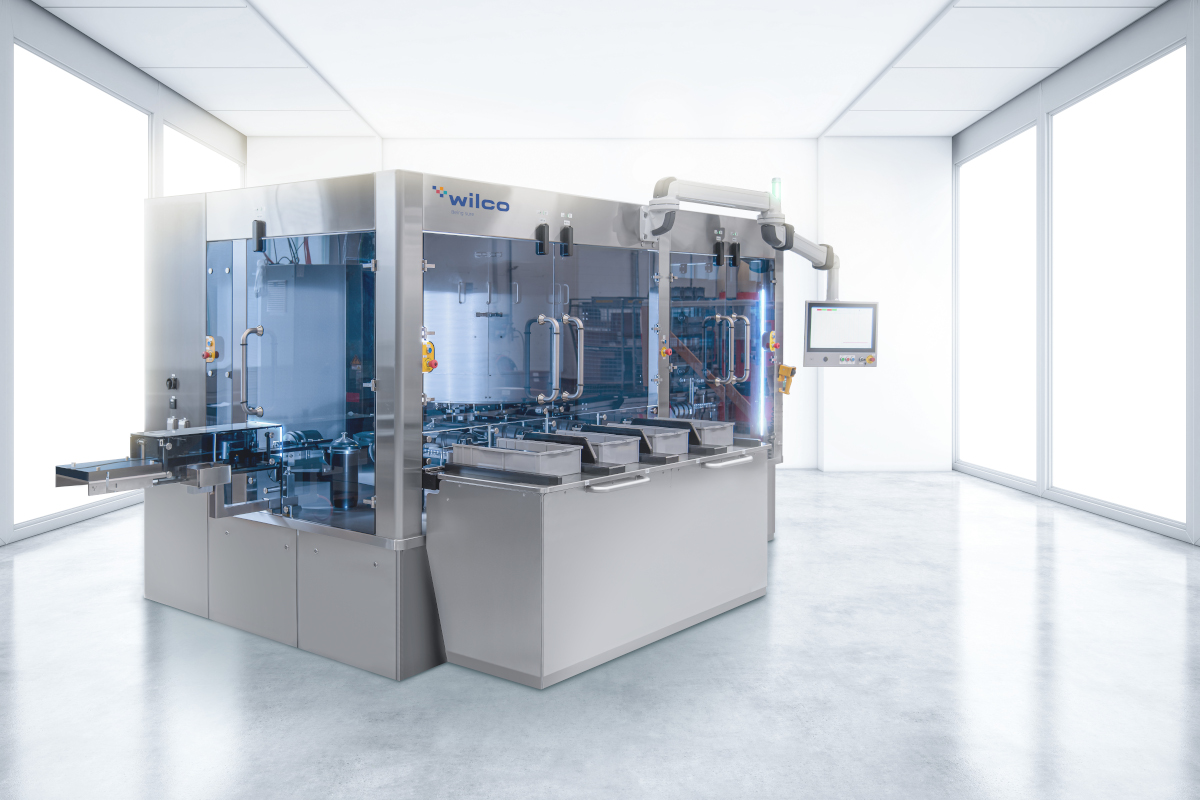
Table of Contents
The pharmaceutical industry relies heavily on efficient and accurate quality control measures. Automated visual inspection of lyophilized vials is critical for ensuring product integrity and patient safety. A single compromised vial can have significant consequences, impacting both the company's reputation and, more importantly, patient health. This comprehensive guide delves into common troubleshooting challenges associated with automated visual inspection systems used for lyophilized vial inspection, providing practical solutions to improve efficiency and accuracy in your pharmaceutical manufacturing process.
Understanding Common Defects in Lyophilized Vials
Keywords: Lyophilized vial defects, particle detection, cracks, delamination, stopper defects, fill level, visual defects, foreign particles.
Identifying and addressing defects in lyophilized vials is paramount. These defects can stem from various stages of the manufacturing process, from freeze-drying (lyophilization) to filling and packaging. Understanding the root cause is crucial for effective corrective action.
-
Identifying common visual defects: Automated visual inspection systems are designed to detect a range of defects, including:
- Cracks in the glass vial itself, indicating potential fragility and leakage.
- Particulate matter – foreign particles within the vial, compromising product sterility.
- Stopper inconsistencies: Stoppers that are dislodged, tilted, or improperly sealed, leading to contamination.
- Insufficient fill level: Vials not filled to the required level, affecting dosage accuracy.
- Vial discoloration: Changes in vial color suggesting degradation or contamination.
- Delamination: Separation of layers within the vial material, a significant structural defect.
-
Understanding the root causes of defects: The origin of these defects can be traced back to several sources:
- Freeze-drying process: Incorrect cycle parameters, equipment malfunction, or inadequate vial preparation can result in cracks, delamination, or uneven freeze-drying.
- Material flaws: Defects in the glass vials or stoppers themselves can be present before the lyophilization process even begins.
- Filling process errors: Contamination, incorrect fill levels, or damaged vials during the filling stage can introduce various defects.
- Damage during transportation and handling: Rough handling can lead to cracks or dislodged stoppers.
-
The importance of accurate defect classification for effective troubleshooting: Differentiating between critical defects (those that directly impact product safety and efficacy) and non-critical defects (those that are aesthetically displeasing but do not pose a significant risk) is essential for prioritizing corrective actions. Accurate classification improves the overall efficiency of your quality control efforts.
Troubleshooting Automated Visual Inspection Systems
Keywords: Automated inspection systems, image processing, algorithm optimization, false positives, false negatives, calibration, system maintenance, sensor issues, lighting, software updates.
Automated visual inspection systems, while highly effective, require regular maintenance and troubleshooting to ensure optimal performance. Issues such as false positives (flagging good vials as defective) and false negatives (missing actual defects) can significantly impact the accuracy of your quality control process.
-
Addressing false positives: False positives can be caused by various factors:
- Optimizing image processing algorithms: Fine-tuning algorithms to better differentiate between actual defects and harmless variations in vial appearance is crucial.
- Adjusting lighting parameters: Incorrect lighting can create shadows or reflections that the system misinterprets as defects. Experimenting with diffused versus direct lighting might improve results.
- Improving system calibration: Regular calibration using standardized vials ensures that the system consistently meets required accuracy levels.
-
Reducing false negatives: False negatives often result from:
- Ensuring adequate sensitivity settings: The system needs to be sensitive enough to detect subtle defects without generating excessive false positives.
- Regular system maintenance: Preventive maintenance, including cleaning sensors and checking for wear and tear, is crucial.
- Inspecting sensor cleanliness and performance: Dirty or malfunctioning sensors will lead to missed defects.
-
Resolving system errors: System errors can stem from various sources:
- Addressing software glitches: Regular software updates and bug fixes are necessary to maintain optimal system performance.
- Hardware malfunctions: Faulty hardware components should be identified and replaced promptly.
- Network connectivity issues: Ensure reliable network connectivity to avoid disruptions to the inspection process.
-
Importance of regular calibration and preventative maintenance: Regular calibration and preventive maintenance are not just recommended; they are essential for extending the lifespan of your system and ensuring accurate, reliable results. A well-maintained system will minimize downtime and improve the overall ROI.
Optimizing Image Acquisition and Processing
Keywords: Image quality, lighting conditions, camera resolution, image analysis algorithms, software parameters, data analysis.
The quality of the images acquired directly impacts the accuracy of defect detection. Optimizing image acquisition and processing parameters is vital for achieving optimal results.
- Selecting the right lighting: The type of lighting significantly impacts defect visibility. Diffused lighting minimizes shadows and reflections, while direct lighting might be more suitable for certain types of defects. Experimentation is key.
- Optimizing camera settings: Properly adjusted camera settings (resolution, exposure, focus) ensure clear and sharp images, enhancing the accuracy of defect detection. High-resolution cameras capture fine details, essential for identifying subtle defects.
- Fine-tuning image analysis algorithms: Adjusting sensitivity parameters within the image analysis software allows for customization to specific defect types. More sensitive settings might be needed for smaller particles.
- Utilizing advanced image processing techniques: Advanced image processing techniques like noise reduction, edge detection, and pattern recognition improve the system's ability to accurately identify and classify defects.
Implementing Effective Quality Control Measures
Keywords: Quality control, GMP compliance, data management, statistical process control (SPC), validation, regulatory compliance, documentation.
Implementing robust quality control measures is critical for ensuring the accuracy and reliability of the automated visual inspection process. This goes beyond just the inspection system itself.
- Implementing robust data management systems for tracking and analyzing inspection results: A comprehensive data management system allows for efficient tracking of inspection results, enabling trend analysis and proactive identification of potential issues.
- Utilizing statistical process control (SPC) techniques to monitor system performance and identify trends: SPC helps monitor the consistency of the inspection process and identifies potential deviations from expected performance.
- Ensuring compliance with Good Manufacturing Practices (GMP) and relevant regulations: Adherence to GMP guidelines and relevant regulatory requirements ensures the integrity of the inspection process and the quality of the final product. This is a critical aspect of pharmaceutical manufacturing.
- Validating the automated inspection system to ensure accuracy and reliability: Formal validation procedures demonstrate that the system meets the required specifications and consistently delivers accurate results.
- Maintaining comprehensive documentation of inspection procedures and results: Detailed documentation of all procedures, results, and maintenance activities is vital for audit trails and regulatory compliance.
Conclusion
Automated visual inspection of lyophilized vials is paramount for maintaining high-quality standards in pharmaceutical manufacturing. By understanding common defects, troubleshooting automated inspection systems, and implementing effective quality control measures, manufacturers can ensure product integrity and patient safety. This guide has provided a framework for addressing challenges and optimizing the performance of automated visual inspection systems. Regular maintenance, careful calibration, and proactive troubleshooting will help you optimize your automated visual inspection processes and minimize the occurrence of defects in your lyophilized vials. Invest in robust automated visual inspection systems and ongoing optimization for efficient and reliable quality control. Don't compromise on quality – choose efficient and accurate automated visual inspection for your lyophilized vials.
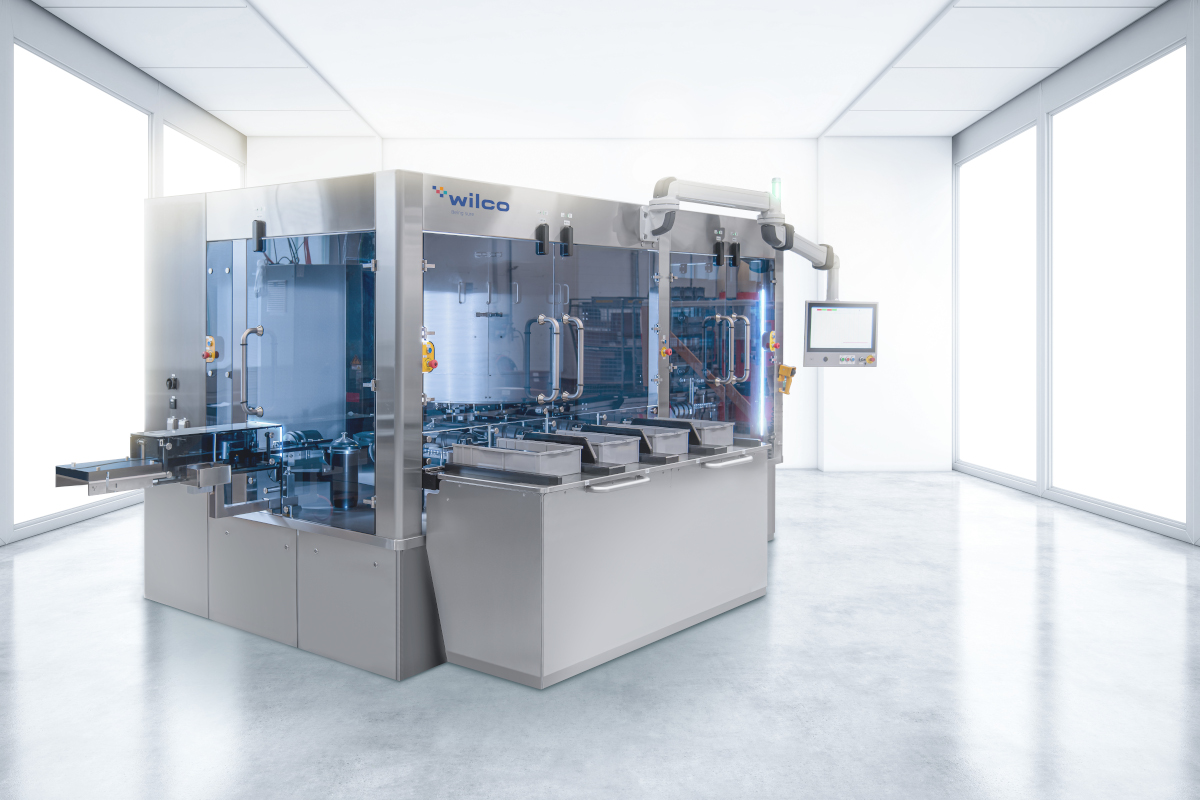
Featured Posts
-
Carrie And The Creatures Boris Johnsons Animal Related Controversies
May 12, 2025 -
Payton Pritchards Rise Factors Contributing To A Breakout Nba Season
May 12, 2025 -
Spor Dzhonsona I Trampa Reyting Zelenskogo 4
May 12, 2025 -
Bayern Munchen Ii Aduce Un Omagiu Lui Thomas Mueller
May 12, 2025 -
Coachella 2025 Tyla Addresses Britney Spears Outfit Comparisons
May 12, 2025
Latest Posts
-
Stallone And Statham Is Stallones Appearance A Setup For A Bigger Role
May 12, 2025 -
Cat A Incasat Sylvester Stallone Pentru Filmele Rocky
May 12, 2025 -
Sylvester Stallone Si Rocky O Analiza Financiara
May 12, 2025 -
Averea Lui Sylvester Stallone Cat A Castigat Din Rocky
May 12, 2025 -
Castigurile Lui Sylvester Stallone Din Franciza Rocky
May 12, 2025