Automated Visual Inspection Of Lyophilized Vials: Challenges And Solutions
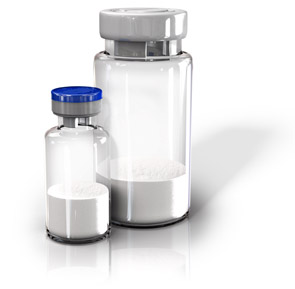
Table of Contents
Challenges in Visual Inspection of Lyophilized Vials
The visual inspection of lyophilized vials presents numerous challenges, impacting both the quality of the final product and the efficiency of the manufacturing process. These challenges stem from inherent variations in the lyophilization process itself, the limitations of human inspectors, and the ever-increasing demands of high-throughput production.
Variations in Lyophilization Processes
Lyophilization is a complex process, and subtle variations in parameters can significantly impact the appearance of the final lyophilized cake. These variations make consistent, reliable manual inspection extremely difficult. Common variations include:
- Variations in cake height: Inconsistent filling levels can lead to uneven cakes, potentially affecting product stability and reconstitution.
- Cracks and fissures: These defects can compromise the integrity of the cake and lead to reduced product quality.
- Cake collapse: Partial or complete collapse of the lyophilized cake indicates problems during the freeze-drying process and may render the product unusable.
- Discoloration: Changes in color can signify chemical degradation or other issues affecting product quality and stability.
These inconsistencies make manual inspection subjective and prone to human error, highlighting the need for a more consistent and objective quality assessment method.
Human Error and Subjectivity
Manual visual inspection of lyophilized vials relies heavily on human judgment, introducing several limitations:
- High throughput demands: Inspecting large numbers of vials manually is time-consuming and leads to bottlenecks in production.
- Operator fatigue: Prolonged visual inspection can lead to inspector fatigue, resulting in decreased accuracy and an increased likelihood of overlooking defects.
- Variations in interpretation: Different inspectors may interpret the same defect differently, leading to inconsistent quality assessment.
- Missed defects: Subtle defects may be missed, particularly during periods of fatigue or due to variations in individual inspector capabilities.
The risk of releasing defective products is significantly increased when relying solely on manual inspection, underscoring the need for a more reliable and objective system.
High Throughput Demands
Modern pharmaceutical manufacturing operates at high volumes, requiring rapid and efficient inspection methods. Manual visual inspection struggles to keep pace with these demands:
- Bottlenecks in production: Manual inspection can create significant bottlenecks, delaying downstream processes and impacting overall production efficiency.
- Increased costs associated with manual inspection: The labor costs associated with manual inspection are substantial, particularly for high-volume production runs.
- Difficulty in scaling up operations: Scaling up manual inspection to meet increasing production demands is both costly and inefficient.
The limitations of manual inspection in high-throughput environments make it clear that automated solutions are necessary to maintain efficiency and product quality.
Solutions Offered by Automated Visual Inspection Systems
Automated visual inspection systems offer a powerful solution to the challenges of manual inspection, providing significant improvements in accuracy, efficiency, and data management.
Improved Accuracy and Consistency
Automated systems leverage advanced image processing techniques such as machine learning and image analysis to provide consistent and objective assessments of lyophilized vials:
- Automated defect detection: Automated systems can detect a wide range of defects, including those too subtle for human inspectors to identify reliably.
- Reduced false positives/negatives: Advanced algorithms minimize errors in detection, leading to more reliable quality assessment.
- Increased sensitivity: Automated systems can detect defects with a much higher degree of sensitivity than manual inspection, improving overall product quality.
These systems utilize sophisticated algorithms to analyze images of each vial, identifying defects with far greater accuracy and consistency than human inspectors.
Increased Throughput and Efficiency
Automation dramatically improves inspection speed, significantly reducing manual labor and accelerating production:
- Higher processing speeds: Automated systems can inspect vials at much higher speeds than human inspectors, eliminating bottlenecks in the production line.
- Reduced inspection time: The overall time required for inspection is significantly reduced, allowing for faster turnaround times and increased production efficiency.
- Efficient handling of large batch sizes: Automated systems can easily handle large batches of vials, ensuring consistent quality control even at high production volumes.
Comparison studies often show that automated systems can increase throughput by several orders of magnitude compared to manual inspection methods.
Data Management and Traceability
Automated visual inspection systems provide detailed records of each inspection, enhancing traceability and regulatory compliance:
- Real-time data acquisition: Data is captured and stored digitally in real-time, enabling comprehensive tracking and analysis of inspection results.
- Improved documentation: Automated systems provide detailed reports and documentation that meet regulatory requirements.
- Integration with manufacturing execution systems (MES): Seamless integration with MES allows for efficient data exchange and process optimization.
- Compliance with regulatory requirements (e.g., 21 CFR Part 11): Automated systems are designed to meet strict regulatory requirements, ensuring data integrity and audit trails.
This improved data management contributes significantly to better quality control and regulatory compliance.
Advanced Imaging Techniques
Modern automated systems employ advanced imaging techniques to enhance defect detection capabilities:
- Multi-spectral imaging: This technique uses multiple wavelengths of light to identify defects that may be invisible to the human eye or standard imaging systems.
- 3D imaging: 3D imaging provides a more comprehensive view of the vial and its contents, allowing for better characterization of defects.
- Enhanced image clarity: Advanced imaging techniques improve the clarity and resolution of images, further increasing the accuracy of defect detection.
- Minimizing false positives and false negatives: The combination of advanced imaging and sophisticated algorithms minimizes errors, ensuring a more reliable inspection process.
These advanced techniques are crucial for detecting subtle defects that might otherwise be missed.
Conclusion
Manual visual inspection of lyophilized vials presents significant challenges, including variations in lyophilization processes, human error, and the demands of high-throughput manufacturing. These limitations increase the risk of releasing defective products and hinder overall production efficiency. Automated visual inspection of lyophilized vials offers a robust solution, providing significant improvements in accuracy, consistency, throughput, and data management. By implementing automated visual inspection systems, pharmaceutical manufacturers can enhance product quality, improve regulatory compliance, and achieve substantial cost savings. To learn more about the specific solutions available to optimize your lyophilization process, we encourage you to explore the latest advancements in automated visual inspection technology and contact a trusted supplier for a consultation. Investing in automated visual inspection systems is an investment in the future of reliable and efficient pharmaceutical manufacturing.
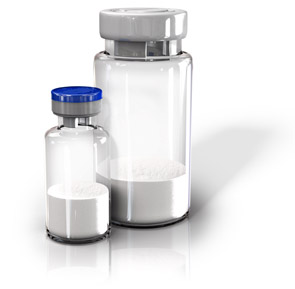
Featured Posts
-
Unveiling Rotorua New Zealands Thriving Geothermal And Cultural Scene
May 12, 2025 -
Knicks Derrotan A Sixers Anunoby Brilla Con 27 Puntos
May 12, 2025 -
Pga Tour Zurich Classic Mc Ilroy And Lowry Commit To Return
May 12, 2025 -
Another Public Appearance Tom Cruise And Ana De Armass Relationship Status Questioned
May 12, 2025 -
Chaplins Crucial Role In Ipswich Towns Success
May 12, 2025
Latest Posts
-
Will Sylvester Stallone Have A Larger Role In Future Jason Statham Films
May 12, 2025 -
Plata Lui Sylvester Stallone Pentru Fiecare Film Rocky
May 12, 2025 -
Stallone And Statham Is Stallones Appearance A Setup For A Bigger Role
May 12, 2025 -
Cat A Incasat Sylvester Stallone Pentru Filmele Rocky
May 12, 2025 -
Sylvester Stallone Si Rocky O Analiza Financiara
May 12, 2025