Challenges And Solutions In Automated Visual Inspection Of Lyophilized Vials
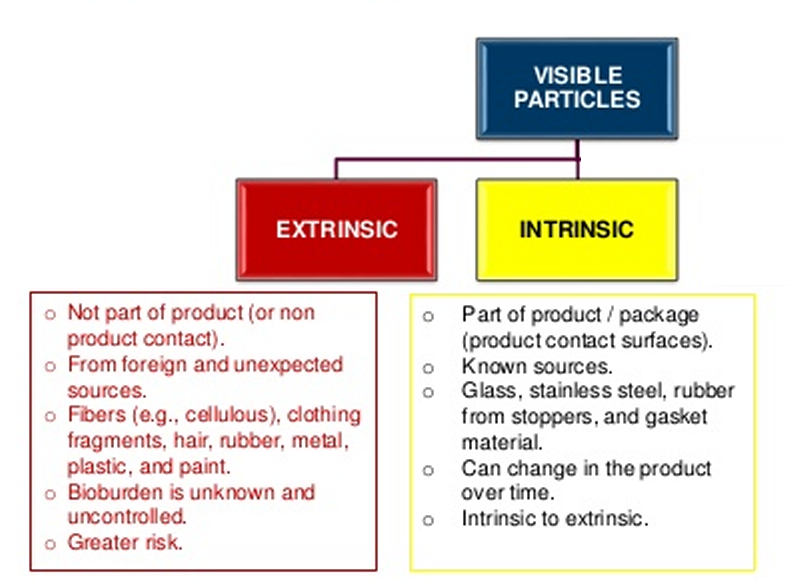
Table of Contents
Challenges in Automated Visual Inspection of Lyophilized Vials
Variations in Vial Appearance and Fill Levels
Lyophilized cakes exhibit inherent variability in appearance. Inconsistencies in the freeze-drying process can lead to cracks, collapses, and non-uniformity in the cake's structure. Similarly, achieving consistent fill levels across all vials is a significant manufacturing challenge. These variations make automated defect detection difficult, leading to a high rate of false positives (rejecting acceptable vials) and false negatives (accepting defective vials). This impacts overall production efficiency and increases costs.
- Examples of visual defects: Cracks, discolorations, particulate matter, incomplete lyophilization, vial breakage, and variations in cake shape and size.
- The subtle nature of some defects necessitates high-resolution imaging and sophisticated algorithms for accurate identification.
Lighting and Image Acquisition Challenges
Achieving consistent and optimal lighting conditions for image acquisition is crucial for accurate automated inspection. Glare, shadows, and reflections from the vial's surface can significantly impact image quality, obscuring defects and leading to misinterpretations. The inherent translucent nature of lyophilized cakes further complicates image acquisition.
- Lighting techniques: Structured light, diffuse lighting, and coaxial lighting are commonly employed, each with its advantages and limitations. The choice depends on the type of defects being detected and the material properties of the vials.
- Technical specifications: High-resolution cameras with appropriate sensitivity and dynamic range, coupled with precisely controlled lighting systems, are essential for optimal results. Considerations include camera sensor type (CMOS or CCD), resolution, and frame rate.
Software and Algorithm Limitations
Developing robust algorithms capable of accurately identifying a wide range of defects in lyophilized vials is a significant challenge. The algorithms must be able to differentiate between acceptable variations in cake appearance and critical defects that compromise product quality. This requires sophisticated image processing techniques that can handle the inherent variability of lyophilized products.
- Algorithm limitations: Difficulty in distinguishing between subtle defects and natural variations, sensitivity to variations in lighting conditions, and limitations in handling complex textures and shapes.
- The use of machine learning and artificial intelligence (AI) is crucial for overcoming these limitations. These techniques enable algorithms to adapt to variations in vial appearance and learn to identify defects more accurately.
Integration and Validation
Integrating automated inspection systems into existing lyophilization manufacturing lines presents logistical challenges. This process requires careful planning and coordination to ensure seamless workflow integration. Furthermore, rigorous validation is essential to ensure the system's accuracy and compliance with regulatory standards, such as 21 CFR Part 11. This validation process is time-consuming and expensive.
- Key aspects of the validation process: Installation Qualification (IQ), Operational Qualification (OQ), and Performance Qualification (PQ). These steps verify that the system is installed correctly, functions as intended, and meets predefined performance criteria.
- Efficient integration necessitates standardized interfaces and communication protocols to minimize disruption to the existing production process.
Solutions for Automated Visual Inspection of Lyophilized Vials
Advanced Imaging Techniques
Employing advanced imaging techniques significantly enhances the accuracy and reliability of automated visual inspection. High-resolution imaging captures fine details, allowing for better defect detection. Multispectral imaging utilizes multiple wavelengths of light to highlight subtle variations in material properties, improving defect identification. 3D imaging provides a comprehensive view of the vial and its contents, enabling the detection of defects that might be missed with 2D imaging.
- Advantages and limitations: High-resolution imaging offers excellent detail but can be computationally intensive. Multispectral imaging can highlight subtle variations but requires specialized equipment. 3D imaging provides comprehensive data but is often more expensive.
Improved Algorithms and AI
Leveraging machine learning and AI algorithms is pivotal in improving the accuracy and adaptability of automated inspection systems. Deep learning models, trained on extensive datasets of images with labeled defects, can learn to recognize complex patterns and subtle variations, leading to improved defect detection accuracy and a reduction in false positives and negatives.
- Examples of AI algorithms: Convolutional Neural Networks (CNNs), Recurrent Neural Networks (RNNs), and Support Vector Machines (SVMs). The selection of the most appropriate algorithm depends on the specific challenges and the available data.
- Regular updates and retraining of AI models are crucial to maintain accuracy and adapt to changes in manufacturing processes.
Optimized System Design and Integration
Careful system design is critical to minimize variability and ensure optimal performance. This involves selecting appropriate hardware components, optimizing lighting conditions, and developing robust algorithms. Seamless integration into existing manufacturing workflows requires standardized interfaces and protocols for data exchange.
- Key design considerations: Modular design for flexibility, ease of maintenance, and scalability; robust error handling mechanisms; and user-friendly interfaces for operation and maintenance.
- Proper planning and collaboration with equipment vendors and integration specialists are crucial for successful implementation.
Optimizing Automated Visual Inspection for Lyophilized Vials: A Path Forward
Automated Visual Inspection of Lyophilized Vials presents unique challenges, from variations in vial appearance to complex algorithm development and system integration. However, by implementing advanced imaging techniques, leveraging AI-powered algorithms, and optimizing system design and integration, manufacturers can significantly improve the accuracy, efficiency, and reliability of their inspection processes. Upgrade your lyophilized vial inspection process by investing in advanced automated visual inspection technologies. Learn more about optimizing your automated visual inspection workflow to ensure consistent product quality and regulatory compliance.
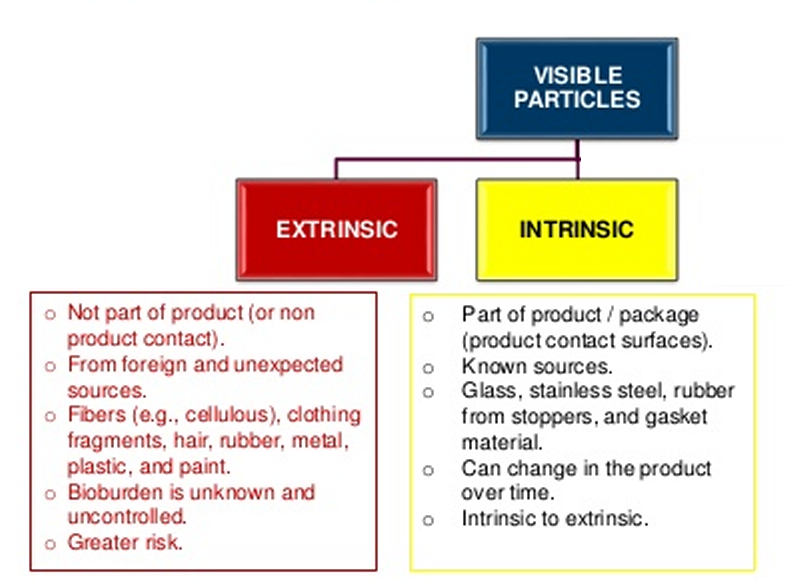
Featured Posts
-
Watch Rory Mc Ilroys Daughters Augusta Putt
May 11, 2025 -
Sissal Represents Denmark At Eurovision 2025 A Deep Dive
May 11, 2025 -
The Untold Story Of Tom Cruises Reaction To Suri Cruises Birth
May 11, 2025 -
Understanding Jurickson Profars 80 Game Ped Suspension
May 11, 2025 -
Santorini Quakes Current Trends And Future Predictions From Scientists
May 11, 2025