Ensuring Quality: Addressing Challenges In Automated Visual Inspection Of Lyophilized Products
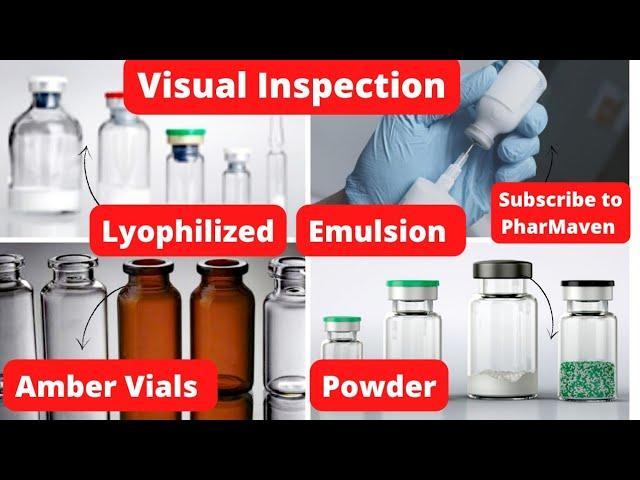
Table of Contents
Image Acquisition Challenges in Automated Visual Inspection of Lyophilized Products
Automated visual inspection (AVI) of lyophilized products faces significant hurdles in image acquisition. The inherent variability of lyophilized cakes and the challenges of capturing high-quality images directly impact the accuracy of defect detection.
Variations in Lyophilized Product Appearance
Lyophilized products often exhibit significant variations in appearance, making consistent image acquisition difficult. This variability stems from numerous factors:
- Differences in cake appearance: Variations in formulation, process parameters (like freeze-drying cycle), and storage conditions can lead to differences in cake appearance, including cracks, fissures, collapse, and variations in color and texture. These subtle variations can confound automated systems designed to detect defects.
- Inconsistent lighting and shadows: Capturing consistent lighting is vital. Shadows and reflections can obscure defects, leading to false negatives. The uneven surface of lyophilized cakes further complicates consistent illumination.
- High-resolution imaging needs: Subtle defects often require high-resolution imaging for accurate detection. The imaging system must be capable of capturing fine details to differentiate between acceptable variations and actual product defects.
Dealing with Reflections and Glare
The glassy nature of many lyophilized products creates significant reflections and glare, masking defects and hindering accurate analysis. This is a major obstacle for reliable automated visual inspection. Mitigating these issues requires specialized techniques:
- Specialized lighting techniques: Using polarized lighting or diffuse lighting can minimize reflections and enhance contrast, improving the visibility of surface defects. Careful control over lighting angles and intensity is crucial.
- Advanced image processing techniques: Software algorithms can be employed to compensate for reflections and glare. Techniques like image enhancement, filtering, and normalization can improve image quality and reduce the impact of reflections.
- Surface treatments: In some cases, applying a surface treatment to the lyophilized product can reduce glare and improve the quality of the acquired images. However, this needs careful consideration to ensure compatibility with the product and its intended use.
Developing Robust Algorithms for Defect Detection in Automated Visual Inspection
Developing algorithms capable of reliably detecting defects in lyophilized products presents a significant challenge. The complexity of lyophilized cake appearance and the need to distinguish defects from natural variations demand sophisticated AI solutions.
Algorithm Training and Data Requirements
Training robust algorithms necessitates extensive, high-quality datasets encompassing a wide range of product variations and defect types. This data must be representative of real-world scenarios to ensure accurate and reliable performance.
- Diverse training datasets: The training dataset needs to include samples from various batches, manufacturing processes, and representing a spectrum of defect severities (from minor cracks to significant collapse).
- Data labeling challenges: Accurately labeling images with defect types and locations is labor-intensive and requires expertise in lyophilized product quality control. The quality of the labeled data directly impacts the performance of the trained algorithm.
- Data augmentation techniques: Techniques like image rotation, scaling, and noise addition can augment the training dataset, improving the robustness and generalization ability of the trained model, particularly valuable when initial data is limited.
Distinguishing Defects from Natural Variations
A crucial challenge is differentiating between genuine defects and acceptable variations in lyophilized product appearance. This requires algorithms capable of handling complex image patterns and nuanced distinctions.
- Sophisticated machine learning algorithms: Advanced machine learning algorithms, such as deep learning models (e.g., convolutional neural networks), are better suited for handling the complexities of image analysis in this context.
- Feature engineering and selection: Carefully selecting and engineering relevant features from the images is critical for algorithm performance. This involves identifying image characteristics that strongly correlate with the presence of defects.
- Deep learning for improved accuracy: Deep learning models can automatically learn complex features from the data, often outperforming traditional machine learning techniques in image classification tasks, particularly when dealing with subtle variations.
Integration and Validation of Automated Visual Inspection Systems
Integrating and validating AVI systems within existing pharmaceutical manufacturing workflows necessitates careful planning and compliance with regulatory requirements.
System Integration and Workflow
Integrating automated visual inspection systems into existing production lines requires careful consideration of several factors:
- Equipment compatibility and data integration: Seamless integration with existing equipment and data management systems is crucial for smooth workflow.
- Robust data management systems: AVI systems generate large volumes of data. Robust data management systems are needed for storage, retrieval, and analysis.
- Validation requirements for regulatory compliance: The system must meet stringent validation requirements for regulatory compliance, like those from the FDA.
Validation and Regulatory Compliance
Validation is paramount to ensure regulatory compliance and reliable performance of automated visual inspection systems. This involves rigorous testing and documentation.
- Meeting regulatory requirements: Systems must meet the stringent requirements of regulatory bodies like the FDA for pharmaceutical manufacturing.
- Rigorous validation protocols: Implementing rigorous validation protocols, including IQ (Installation Qualification), OQ (Operational Qualification), and PQ (Performance Qualification), is essential to demonstrate system accuracy and reliability.
- Ensuring traceability and data integrity: Maintaining complete traceability and data integrity throughout the inspection process is critical for regulatory compliance and troubleshooting.
Conclusion
Automated visual inspection of lyophilized products offers significant advantages in terms of efficiency and quality control, reducing human error and increasing throughput. However, overcoming the challenges related to image acquisition, algorithm development, and system integration is essential for successful and reliable implementation. By focusing on improving data acquisition techniques, developing sophisticated AI algorithms, and ensuring proper system validation, the pharmaceutical industry can leverage the benefits of automated visual inspection to enhance the quality and consistency of lyophilized products. Investing in robust and validated automated visual inspection systems is crucial for ensuring the quality and safety of lyophilized pharmaceuticals. Don't compromise on quality—explore solutions for improving your automated visual inspection of lyophilized products today!
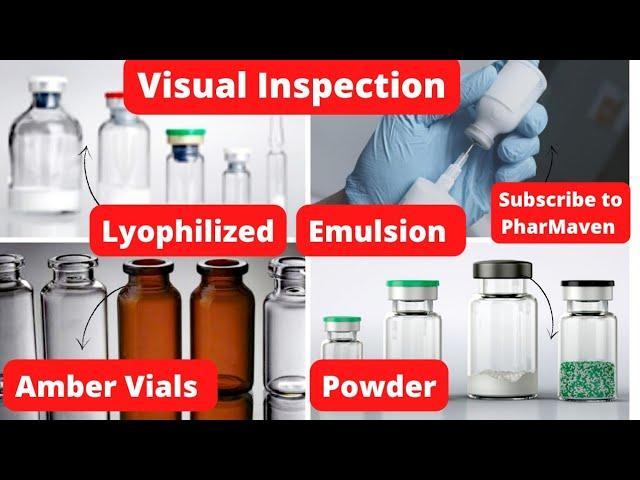
Featured Posts
-
Newark Airports Ongoing Tech Issues Cause Widespread Flight Disruptions
May 11, 2025 -
Sylvester Stallone Action Thriller Armor Now Streaming Free This Month
May 11, 2025 -
Shevchenko Open To Zhang Weili Showdown Will The Superfight Happen
May 11, 2025 -
Undeterred Sheehans Post Match Interview Ipswich Town
May 11, 2025 -
Jessica Simpsons New Song Hints At Eric Johnson Infidelity
May 11, 2025