Improving Automated Visual Inspection For Lyophilized Vials
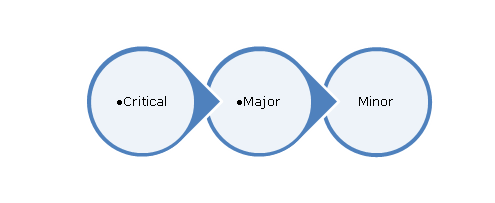
Table of Contents
Challenges in Manual Visual Inspection of Lyophilized Vials
Manual visual inspection of lyophilized vials presents several significant challenges that impact both product quality and production efficiency. These challenges necessitate a shift towards more advanced, automated systems.
Subjective Assessment and Human Error
Manual inspection relies heavily on human judgment, introducing subjectivity and inconsistency. This leads to a higher risk of defects being overlooked, potentially resulting in compromised product quality and costly recalls.
- Fatigue: Inspectors can experience fatigue during long shifts, leading to decreased vigilance and a higher rate of missed defects.
- Inconsistencies between inspectors: Different inspectors may have varying interpretations of acceptable quality standards, leading to discrepancies in defect detection.
- Difficulty detecting subtle defects: Subtle defects like hairline cracks, particulate matter, or minor discoloration can be easily missed by the human eye.
The high cost associated with human error is substantial. Rejected batches, product recalls, and the associated regulatory penalties can significantly impact a company's bottom line. A single recall can cost millions of dollars and severely damage a company's reputation.
Bottlenecks in Production
Manual visual inspection is a significant bottleneck in lyophilized vial production lines. The slow, labor-intensive process significantly reduces throughput and impacts overall manufacturing output.
- Reduced throughput: Manual inspection dramatically slows down the production line, limiting the number of vials that can be processed in a given timeframe.
- Increased labor costs: A large workforce is required for manual inspection, leading to higher labor costs and increased overhead.
- Extended lead times: The slower processing speed extends the overall lead time for order fulfillment, potentially impacting customer satisfaction and market competitiveness.
The impact of these bottlenecks is significant. For example, a production line processing 10,000 vials per day might see a 20% reduction in throughput due to manual inspection, resulting in a loss of 2,000 vials daily. This translates to lost revenue and potential delays in meeting market demands.
Difficulty in Maintaining Consistent Quality Standards
The inherent variability in human performance makes it challenging to maintain consistent quality standards during manual inspection. This inconsistency increases the risk of releasing defective products.
- Lack of standardized procedures: Without standardized procedures, inspectors may follow different methods, leading to variations in inspection effectiveness.
- Difficulty documenting inspection findings: Manual documentation is time-consuming and prone to errors, making it difficult to track defect trends and identify root causes.
- Inconsistent application of acceptance criteria: Variations in the application of acceptance criteria by different inspectors lead to inconsistent quality control.
Maintaining regulatory compliance is paramount in the pharmaceutical industry. Inconsistent quality control practices can result in non-compliance, leading to regulatory actions, fines, and reputational damage.
Advanced Technologies for Automated Visual Inspection
Advanced technologies offer a solution to the challenges of manual inspection, providing faster, more accurate, and consistent results.
Computer Vision Systems and Image Processing
Computer vision systems leverage advanced algorithms and machine learning to automatically detect defects in lyophilized vials. These systems utilize high-resolution imaging and sophisticated image processing techniques for precise defect identification.
- High-resolution imaging: High-resolution cameras capture detailed images of each vial, allowing for the detection of even subtle defects.
- Automated defect classification: Advanced algorithms automatically classify and categorize defects, providing detailed information about the type and severity of each defect.
- Real-time analysis: Real-time analysis enables immediate feedback, allowing for immediate adjustments to the production process to prevent further defects.
- Data analytics for process optimization: Collected data provides valuable insights into defect trends, allowing for proactive process improvements and optimization.
Computer vision systems, employing techniques like convolutional neural networks (CNNs), can identify defects like cracks, particulate matter, and fill level inconsistencies with far greater accuracy and consistency than human inspectors.
Integration with Automated Packaging Lines
Seamless integration of automated visual inspection systems into high-speed packaging lines is crucial for maximizing efficiency. This integration ensures continuous and uninterrupted processing.
- Increased throughput: Automated inspection significantly increases the throughput of the production line, resulting in higher output.
- Reduced downtime: Automated systems minimize downtime associated with manual inspection, leading to increased overall productivity.
- Improved overall efficiency: Streamlined integration improves the overall efficiency of the entire production process.
Careful consideration must be given to system compatibility and data exchange between different equipment within the production line to ensure smooth integration and optimal performance.
Benefits of Implementing Automated Systems
Implementing automated visual inspection systems offers significant returns on investment (ROI) through substantial cost savings and improved product quality.
- Reduced labor costs: Automation reduces the need for a large workforce dedicated to manual inspection, leading to significant cost savings.
- Improved product quality: Automated systems provide higher accuracy and consistency in defect detection, resulting in improved product quality and reduced recalls.
- Increased throughput: Automated systems significantly increase production throughput, leading to higher production output and revenue.
- Enhanced regulatory compliance: Improved consistency and accuracy in quality control enhance regulatory compliance, reducing the risk of penalties and reputational damage.
Quantifiable benefits can be substantial. For example, a company might experience a 50% reduction in human error, a 30% increase in production output, and a 20% reduction in labor costs after implementing an automated visual inspection system.
Key Considerations for Successful Implementation
Successful implementation of an automated visual inspection system requires careful planning and consideration of several key factors.
System Validation and Qualification
Rigorous validation and qualification processes are essential to ensure the accuracy and reliability of the automated system. This is crucial for meeting regulatory requirements and maintaining product quality.
- IQ/OQ/PQ validation: Installation Qualification (IQ), Operational Qualification (OQ), and Performance Qualification (PQ) are critical steps to verify that the system is installed, operates, and performs as intended.
- Performance verification: Regular performance verification ensures the system's ongoing accuracy and reliability.
- Regulatory compliance (e.g., 21 CFR Part 11): The system must comply with all relevant regulatory requirements, including data integrity and audit trail requirements.
The validation process involves detailed documentation and testing to demonstrate the system's ability to meet predefined performance criteria. This is crucial for regulatory compliance and for building confidence in the system's accuracy.
Data Management and Analysis
Efficient data management and analysis are critical for continuous improvement and proactive quality control. The data generated by the automated system provides valuable insights into production processes.
- Data logging: Automated data logging provides a detailed record of all inspections, defects, and production parameters.
- Trend analysis: Analysis of historical data can identify trends and patterns in defect occurrence, enabling proactive mitigation strategies.
- Root cause analysis: Detailed data allows for in-depth root cause analysis of defects, leading to targeted process improvements.
- Predictive maintenance: Data analysis can predict potential equipment failures, enabling proactive maintenance and minimizing downtime.
Effective data management and analysis are key to optimizing the inspection process and maximizing the benefits of automated visual inspection.
Choosing the Right Automated Visual Inspection System
Selecting the right automated visual inspection system requires careful consideration of several factors based on specific production needs and budget constraints.
- Throughput requirements: The system should be capable of handling the required production throughput.
- Image resolution: High-resolution imaging is crucial for detecting subtle defects.
- Defect detection capabilities: The system should be capable of detecting all relevant defects.
- Integration with existing equipment: Seamless integration with existing equipment is essential for efficient operation.
- Budget: The budget should be carefully considered when selecting a system.
Careful evaluation of available systems and thorough consultation with vendors are necessary to select the most suitable system for specific requirements.
Conclusion
Improving automated visual inspection for lyophilized vials is crucial for enhancing efficiency, ensuring product quality, and meeting regulatory requirements. By adopting advanced technologies like computer vision and machine learning, pharmaceutical manufacturers can overcome the limitations of manual inspection and achieve significant improvements in their production processes. Investing in a robust automated system offers substantial returns through reduced costs, improved throughput, and enhanced product quality. Contact us today to discuss how we can help you optimize your automated visual inspection for lyophilized vials.
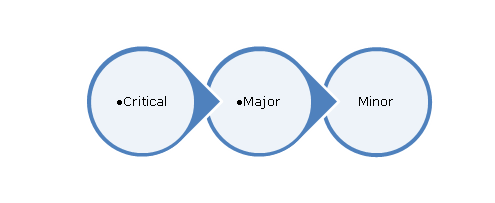
Featured Posts
-
Who Might Succeed Pope Francis Potential Candidates For The Papacy
May 11, 2025 -
Get Ready The John Wick Experience Launches In Las Vegas
May 11, 2025 -
Pope Leo Is Inaugural Mass A Call To Counter De Facto Atheism
May 11, 2025 -
Celtics Unlikely Duo 40 Point Games In One Night
May 11, 2025 -
Former Ufc Champion Aldos Featherweight Return A Fighters Comeback Story
May 11, 2025