Strategies For Efficient Automated Visual Inspection Of Lyophilized Drug Products
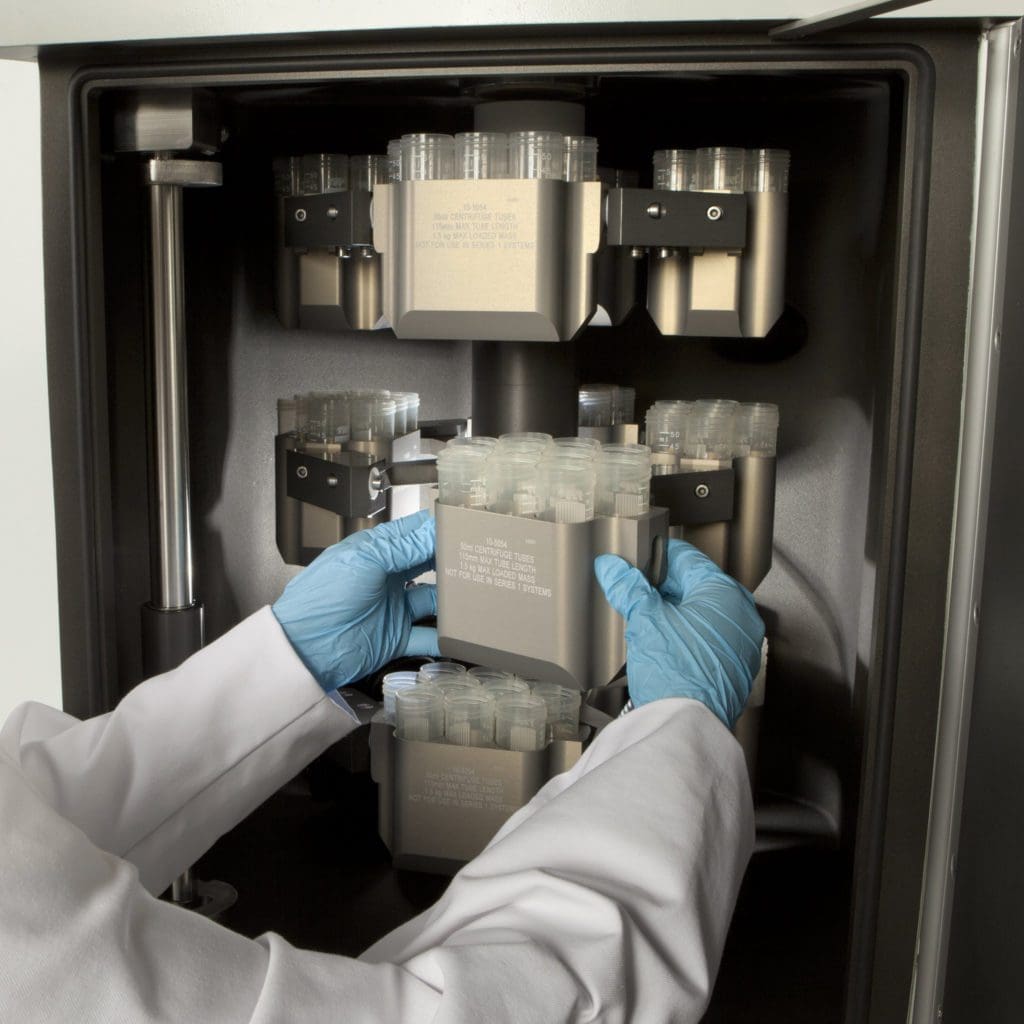
Table of Contents
Selecting the Right Automated Visual Inspection System for Lyophilized Products
Choosing the right automated visual inspection system is paramount for successful implementation. Several technologies exist, each with its strengths and weaknesses regarding lyophilized drug product inspection.
- 2D Imaging Systems: These systems utilize a single camera to capture 2D images of the product. They are cost-effective but may struggle with complex three-dimensional defects.
- 3D Imaging Systems: Employing multiple cameras or structured light, these systems create 3D models of the product, enabling the detection of defects hidden from a single viewpoint. This is particularly beneficial for identifying cracks or inconsistencies in the cake structure of lyophilized vials.
- Hyperspectral Imaging: This advanced technique captures images across a wide range of wavelengths, providing spectral information in addition to visual data. This can be used to detect subtle variations in chemical composition or identify defects invisible to standard imaging techniques.
Key considerations when selecting a system include:
- Resolution and Sensitivity: The system must offer sufficient resolution to detect even minute defects like cracks, discoloration, or particulate matter. High sensitivity is crucial for identifying subtle flaws.
- Throughput and Processing Speed: The system's speed must match your production demands, ensuring efficient processing without bottlenecks. High-throughput systems are essential for large-scale manufacturing.
- Integration Capabilities: Seamless integration with your existing manufacturing equipment and existing data management systems (MES, LIMS) is vital for streamlined workflow.
- Data Management and Analysis Features: Robust data management and sophisticated analysis capabilities are essential for tracking quality trends, identifying potential problems early, and fulfilling regulatory reporting requirements.
- Regulatory Compliance and Validation: The system must meet all relevant regulatory requirements, such as 21 CFR Part 11, and be readily validated to ensure data integrity and reliability. Consider systems with built-in features to facilitate validation processes.
Successful implementations often leverage systems from leading providers in the pharmaceutical automation sector, adapting their solutions to the specific challenges of lyophilized product inspection.
Optimizing Image Acquisition and Processing for Lyophilized Drug Products
Imaging lyophilized products presents unique challenges. The variations in surface texture, light scattering, and the inherent fragility of the product can complicate defect detection. Optimizing both image acquisition and processing is crucial for accurate and reliable results.
Optimizing Image Acquisition:
- Lighting Techniques: Structured lighting techniques, combined with diffuse lighting, effectively enhance defect visibility by minimizing shadows and highlighting surface irregularities.
- Camera Selection and Positioning: Selecting cameras with appropriate resolution, sensitivity, and depth of field is crucial. Optimal camera positioning minimizes distortion and maximizes defect visibility.
- Calibration Procedures: Regular calibration ensures accurate measurements and consistent image quality over time.
Image Processing Techniques:
- Image Filtering and Enhancement: Algorithms such as noise reduction, edge enhancement, and contrast adjustment improve image quality, making defect detection easier.
- Defect Classification and Segmentation: Machine learning algorithms can be trained to identify and classify various defects, automating the analysis process and improving accuracy.
- False Positive Reduction: Sophisticated algorithms and careful training of machine learning models can minimize false positives, reducing the need for manual intervention.
Implementing and Validating Automated Visual Inspection Systems
Thorough validation is crucial to ensure the automated visual inspection system meets regulatory requirements and provides reliable results. This involves a multi-step process:
- Installation Qualification (IQ): Verifying that the system is correctly installed and configured according to manufacturer specifications.
- Operational Qualification (OQ): Demonstrating that the system operates as intended under defined conditions.
- Performance Qualification (PQ): Showing the system consistently meets predetermined performance criteria and accurately detects defects.
Ongoing monitoring and maintenance are vital for continued accuracy and reliability. Regular calibration, preventative maintenance, and software updates are essential. Furthermore, integrating the automated visual inspection data with other quality control systems (e.g., manufacturing execution systems – MES) provides a holistic view of the production process, enabling proactive quality management. Data analysis can reveal trends and pinpoint potential process improvements.
Advanced Techniques and Future Trends in Automated Visual Inspection
The field of automated visual inspection is constantly evolving. Emerging technologies promise even greater accuracy and efficiency.
- AI and Machine Learning: These technologies offer the potential to significantly improve defect detection accuracy by learning from vast datasets of images, adapting to variations in product appearance, and reducing false positives.
- Hyperspectral Imaging: Beyond visual inspection, hyperspectral imaging allows analysis of the chemical composition of lyophilized products, identifying subtle defects undetectable by traditional methods. This offers enhanced quality control and a deeper understanding of the product's integrity.
- Integration with Lyophilization Process: Future trends indicate the integration of automated visual inspection with other automated systems within the lyophilization process, leading to fully automated, closed-system production lines with increased efficiency and reduced contamination risk.
Maximizing Efficiency with Automated Visual Inspection of Lyophilized Drug Products
Implementing Automated Visual Inspection of Lyophilized Drug Products offers significant advantages. By selecting the right system, optimizing image acquisition and processing, and ensuring thorough validation, pharmaceutical manufacturers can maximize efficiency, improve product quality, reduce costs associated with manual inspection, and achieve enhanced regulatory compliance. The benefits are clear: increased throughput, improved accuracy, reduced human error, and better data analysis leading to more informed decision-making.
To improve your lyophilized drug product quality control and efficiency, explore the benefits of implementing Automated Visual Inspection for Lyophilization today. Consider conducting further research or contacting providers of efficient automated lyophilized product inspection systems to discuss solutions tailored to your specific needs.
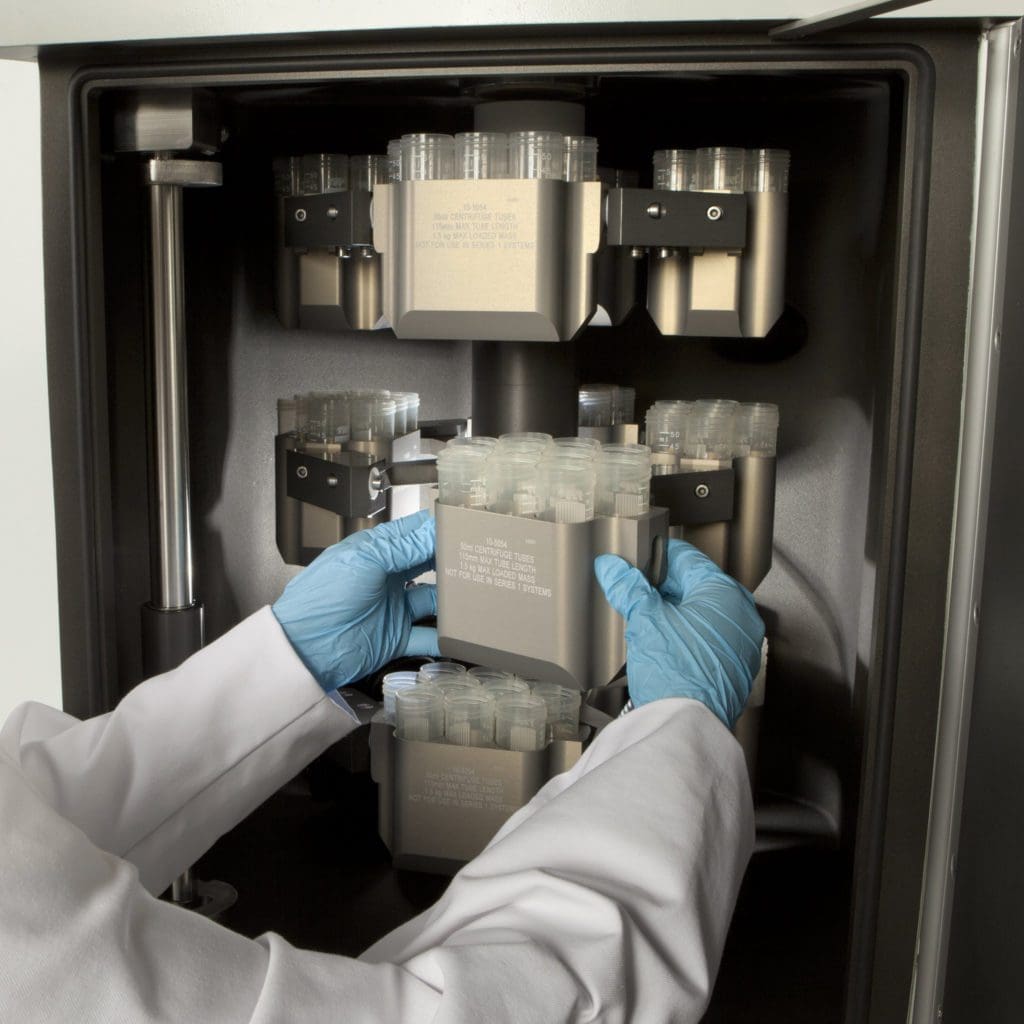
Featured Posts
-
La Inusual Estrategia De Uruguay Para Mejorar Las Exportaciones Ganaderas A China
May 12, 2025 -
Jessica Simpson Sparks Reality Tv Rumors Amidst New Album Release
May 12, 2025 -
Jose Aldo De La Deception A La Motivation Son Histoire
May 12, 2025 -
Planning Your Meeting With Shane Lowry
May 12, 2025 -
Ufc 315 Complete Main Card Unveiled Featuring Muhammad Vs Della Maddalena
May 12, 2025
Latest Posts
-
Impactul Financiar Al Lui Rocky Asupra Carierei Lui Sylvester Stallone
May 12, 2025 -
Analiza Financiara Castigurile Lui Sylvester Stallone Din Rocky
May 12, 2025 -
Banii Lui Sylvester Stallone Contributia Filmelor Rocky
May 12, 2025 -
Succesul Financiar Al Lui Sylvester Stallone Din Seria Rocky
May 12, 2025 -
Analyzing Sylvester Stallones Limited Role In Jason Stathams Latest Action Movie
May 12, 2025