The Fight For American Factory Jobs: Who Will Fill Them?
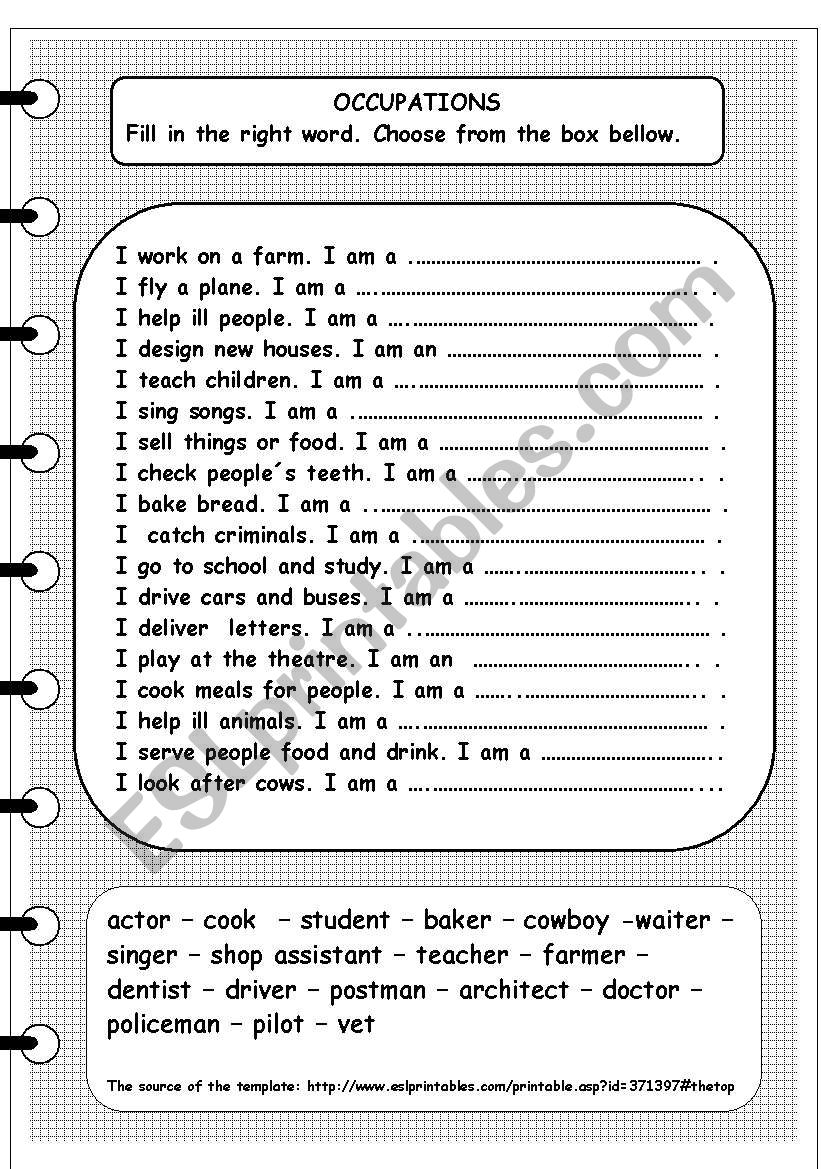
Table of Contents
The Shrinking Skilled Labor Pool
The shortage of skilled workers in American factories is a multifaceted problem stemming from several interconnected issues. The resulting skills gap threatens the long-term health and prosperity of the manufacturing sector.
The Aging Workforce
- The Statistic: The average age of factory workers in the US is steadily rising, with a significant portion of the workforce nearing retirement age. Many experienced technicians and machinists are retiring without adequate replacements.
- Reasons for Aging Workforce: The decline in apprenticeships and vocational training programs has contributed to a significant drop in younger individuals entering the field. Additionally, negative perceptions of factory work as dirty, dangerous, and low-paying have deterred many from pursuing careers in manufacturing.
- Impact on Production: This mass exodus of experienced workers directly impacts production capacity, potentially leading to delays, increased costs, and a reduction in overall output. The loss of institutional knowledge is also a major concern.
Lack of Vocational Training
- Past vs. Present: In the past, vocational schools and apprenticeships provided a robust pipeline of skilled workers for manufacturing. Today, the emphasis on higher education has often overshadowed these crucial pathways.
- Impact of Higher Education Push: While a college degree is valuable, the push towards higher education has inadvertently reduced the number of individuals pursuing trade skills, leaving a void in the skilled labor market.
- Reskilling and Upskilling Initiatives: The need for reskilling and upskilling programs is critical. These programs can help bridge the gap by training individuals with existing skills for advanced manufacturing roles or providing pathways for those entering the field for the first time.
Negative Perceptions of Factory Work
- Outdated Stereotypes: Many still harbor outdated stereotypes of factory work, associating it with repetitive, dangerous, and low-paying jobs. This perception needs to be dramatically altered.
- Modern, High-Tech Factories: Modern factories are increasingly incorporating advanced technologies, creating sophisticated, high-skill jobs requiring advanced training and problem-solving abilities.
- Improved Safety Measures: Significant advancements in workplace safety have greatly reduced the risks associated with factory work, improving the working conditions considerably.
- Career Advancement Opportunities: Many manufacturing companies offer opportunities for professional development, skill enhancement, and career advancement, allowing employees to climb the ladder within the organization.
Attracting and Retaining a New Generation of Workers
Addressing the shortage of skilled workers requires a multi-pronged approach focusing on making these jobs attractive and ensuring employee retention.
Improving Wages and Benefits
- Competitive Compensation: Attracting top talent requires offering competitive wages and benefits packages that are comparable to, or better than, those offered in other sectors.
- Successful Strategies: Some companies have successfully implemented profit-sharing plans, comprehensive healthcare benefits, and tuition reimbursement programs to attract and retain employees.
- Impact of Benefits on Retention: A strong benefits package not only attracts new hires but also significantly improves employee retention rates, reducing the costs associated with constant recruitment and training.
Investing in Technology and Automation
- Automation's Role: The integration of robotics and automation in factories can significantly reduce the need for repetitive and physically demanding tasks, making the work environment more appealing.
- Creating Higher-Skilled Jobs: Automation often creates a need for higher-skilled workers to operate, maintain, and program these advanced systems. This shift creates new, more attractive roles.
- Improved Safety: Robots can handle dangerous tasks, reducing workplace accidents and creating a safer working environment.
Promoting a Positive Work Culture
- Strong Company Culture: A positive and inclusive work environment, characterized by open communication, mutual respect, and opportunities for growth, significantly increases employee satisfaction and retention.
- Employee Well-being: Companies prioritizing employee well-being through wellness programs, flexible work arrangements, and work-life balance initiatives attract and retain valuable workers.
- Strategies for Improved Engagement: Investing in employee training, providing regular feedback, and offering opportunities for advancement significantly improve employee engagement.
Government Initiatives and Industry Collaboration
Addressing the shortage of skilled workers requires collaboration between government agencies, educational institutions, and the manufacturing industry itself.
Government Funding for Vocational Training
- Investing in Education: Government funding for vocational training programs and apprenticeships is crucial for creating a pipeline of skilled workers. This includes funding for equipment, curriculum development, and instructor training.
- Successful Programs: Examples of successful government-funded programs should be highlighted and promoted to encourage further investment and collaboration.
- Policy Recommendations: Advocating for policies that prioritize vocational education and create incentives for individuals and companies to participate in training programs is essential.
Industry Partnerships and Workforce Development
- Collaboration is Key: Strong partnerships between manufacturers and educational institutions are vital for developing relevant training programs that meet the specific needs of the industry.
- Industry-Led Training: Industry-led training programs that provide hands-on experience and connect job seekers directly with employers are highly effective.
- Connecting Job Seekers: Creating platforms and initiatives that effectively connect job seekers with available positions in manufacturing is crucial to filling open roles.
Conclusion
The shortage of skilled workers in American factories presents a significant challenge to the nation's economic future. Addressing this skills gap requires a concerted effort from various stakeholders, including government, educational institutions, and the manufacturing industry itself. By investing in vocational training, improving wages and benefits, embracing technology, and fostering a positive work culture, we can attract and retain a new generation of workers for American factory jobs.
To contribute to this vital effort, consider researching local apprenticeship programs, contacting manufacturing companies directly to learn about available opportunities, or advocating for policies that support vocational education and workforce development initiatives. The future of American manufacturing depends on our ability to fill these crucial American factory jobs and secure a strong and competitive manufacturing sector.
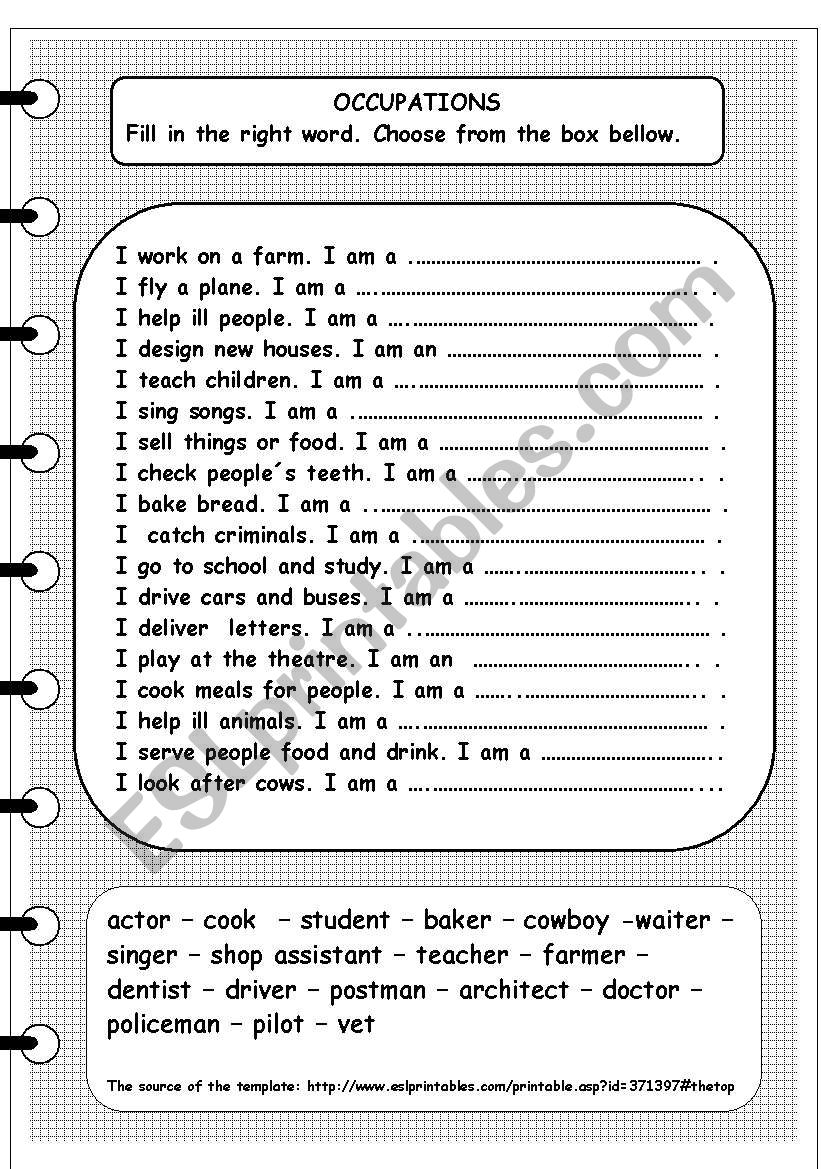
Featured Posts
-
Proposed Texas Legislation Would Limit Teen Social Media Use
May 20, 2025 -
Analyzing The Risks Of The Philippine Typhon Mid Range Missile System
May 20, 2025 -
Offerta Lampo Hercule Poirot Su Play Station 5 A Prezzo Scontato Meno Di 10 E
May 20, 2025 -
Dzhennifer Lourens Znovu Stala Mamoyu
May 20, 2025 -
Andelka Milivojevic Tadic Emotivno Oprostili Se Od Legendarne Glumice
May 20, 2025